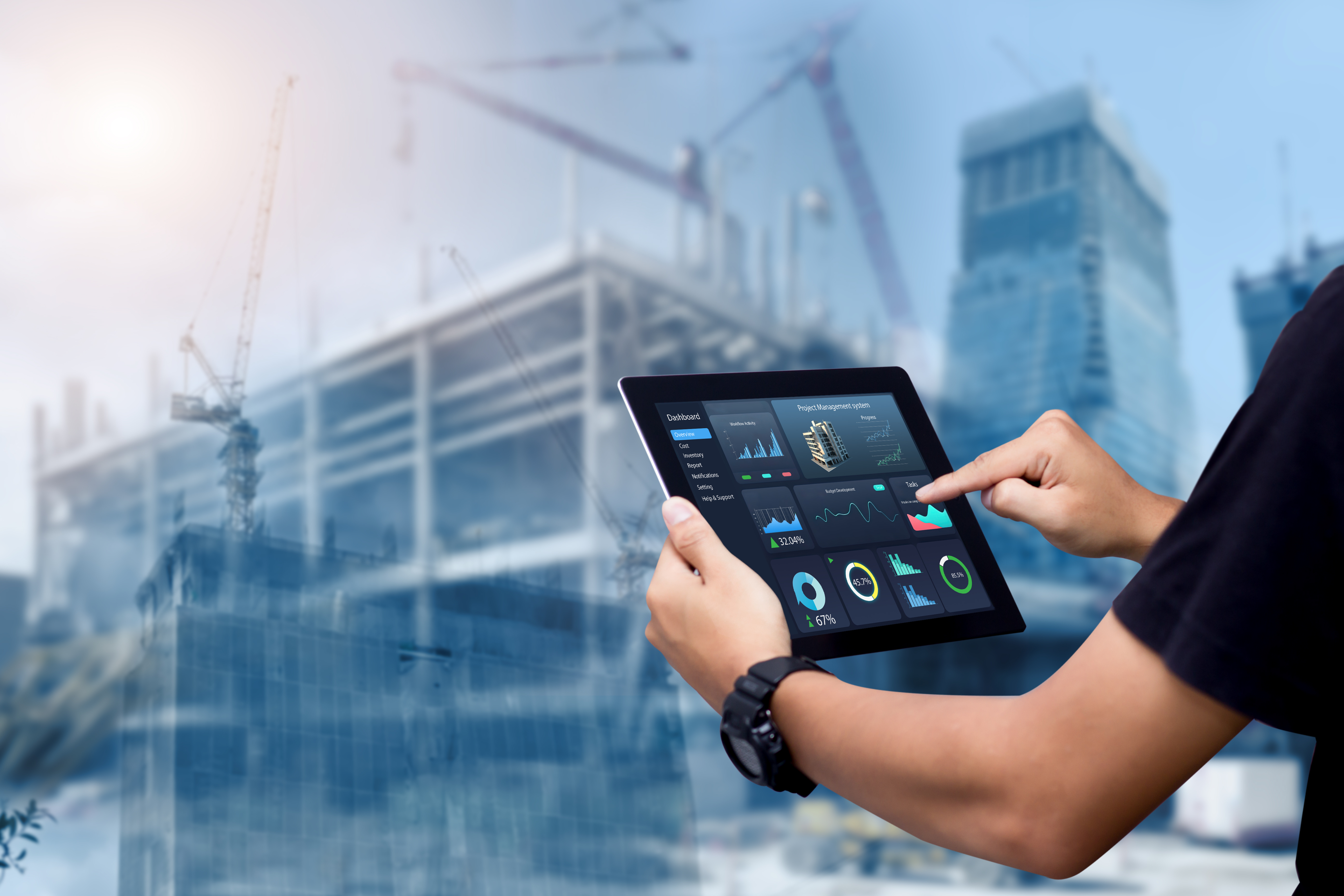
THE SIGNIFICANCE OF SUPPLY CHAIN RISK TO CONSTRUCTION COMPANIES
Supply chain issues are one of the biggest concerns for Canadian construction companies today. In a January 2023 survey by the Association of Independent Contractors and Trades, 58% of Canadian construction companies said they expect supply chain issues to be a challenge in 2023.1 Only the lack of skilled labor was cited more often. This follows earlier survey results for 2022, where 76% of companies reported delays in supplying construction materials for their projects. Construction companies were also asked in the January 2023 survey about the effects of material shortages on their business. More than 80% of the companies had to delay project completion times due to long waiting times for materials. Almost 25% turned down new job opportunities because they could not get the necessary inputs to complete the project, as shown in Figure 1. Another way to identify the impact of supply chain deficiencies on construction companies is to run the scenario in a large-scale macroeconomic model. The results show that Canadian construction output in 2022 was 2 percent lower than it otherwise would have been as companies struggled to fulfill ongoing contracts and obtain materials needed for new ones. The results of the 2023 scenario show that supply disruptions are likely to reduce construction output by 1½ below what it would otherwise have been.
Canada imports nearly 20% of its total construction inputs from China. This dependence on China is greater than that of Canada’s European counterparts (Germany, France, Spain, Italy, the United Kingdom and the Nordic countries). Countries around the world are still facing supply chain disruptions due to China’s Covid-19 policies and continued escalation in geopolitical tensions could cause further problems even if China loosens restrictions.
Reliance on one or a few countries is not the only potential bottleneck in Canada’s supply chain. The same applies to the mode of transportation of imported materials. For trade with the United States, this is usually not an issue, as most goods are transported by land. However, Canadian trucker strikes in 2022 over mandatory Covid vaccinations have demonstrated that, despite being considered a safe mode of transport, disruption is always possible. However, imports from China and other countries will enter by sea or air. For example, the proportion of the following inputs imported by sea is:
wooden floors (81%), processed marble (85%) and concrete iron (70%). If air or sea routes — or freight hubs — fail, Canadian construction companies could find themselves without essential supplies.
Actions Construction Companies Can Do to Reduce Supply Chain Risks?
Companies can invest resources in gathering market intelligence and developing relationships with other vendors available to them. The ability to flexibly transfer operations to different vendors offsets some of the risks of being too dependent on a single supplier if unforeseen challenges arise. The same is true for different modes of transport or specific routes and hubs (such as ports) for imports and imports from different geographical areas. Having contingency plans in place for negative situations can be beneficial.
Forward-thinking companies can use recent commodity price spikes as a turning point in how they structure their contracts. Being tied to fixed-price contracts during times of economic uncertainty and large price fluctuations can lead to projects that end up losing money. The standard adoption of cost escalation clauses avoids this problem, by allowing companies to share the additional costs incurred when input prices rise.
Deploying technology throughout the supply chain to integrate previously separate processes can be a source of competitive advantage for companies, by streamlining and simplifying material sourcing. and input. In addition, technology can be used to eliminate human error. For example, set up a system that automatically places orders when inventory reaches a certain level.
Finally, companies may need to review the method they use to manage their supply chain schedules. In times of economic stability, “just in time” has proven to be effective in reducing inventory levels and storage costs. However, in unpredictable times, the “just in case” approach to maintaining higher inventory levels can be a safer option. If supply chains are disrupted and inputs become hard to buy, companies that hold larger inventories will be in a better position to continue operating.